Working Methodology
Project Practicability
First contact and evaluation of project feasability.
Analysis
Risk assessment and establishment of the conduct of the entire project
Machinery
Delivery and installation of the machinery
Floor and Ceiling
Delivery and assembly of the floor and ceiling
Commissioning
Software tuning and overall supervision of the entire installation

Project Practicability
Provided with sufficient data on the project, we are able to estimate the feasibility and the price of the system. The information required is as follows :
- Lounge dimensions (including usable height)
- Information on the upper and lower floors
- Total number of floors in the building
- Information on the technical room
Analysis
For existing constructions the risk assessment and building analysis require an on site visit from our engineering team (If the edifice is not built yet, we will work with blueprints). We will then implement a guideline for the project consisting of :
- Required specifications
- Checklist with benchmark measurements
- Block diagram
- Design of the built-in monitoring software
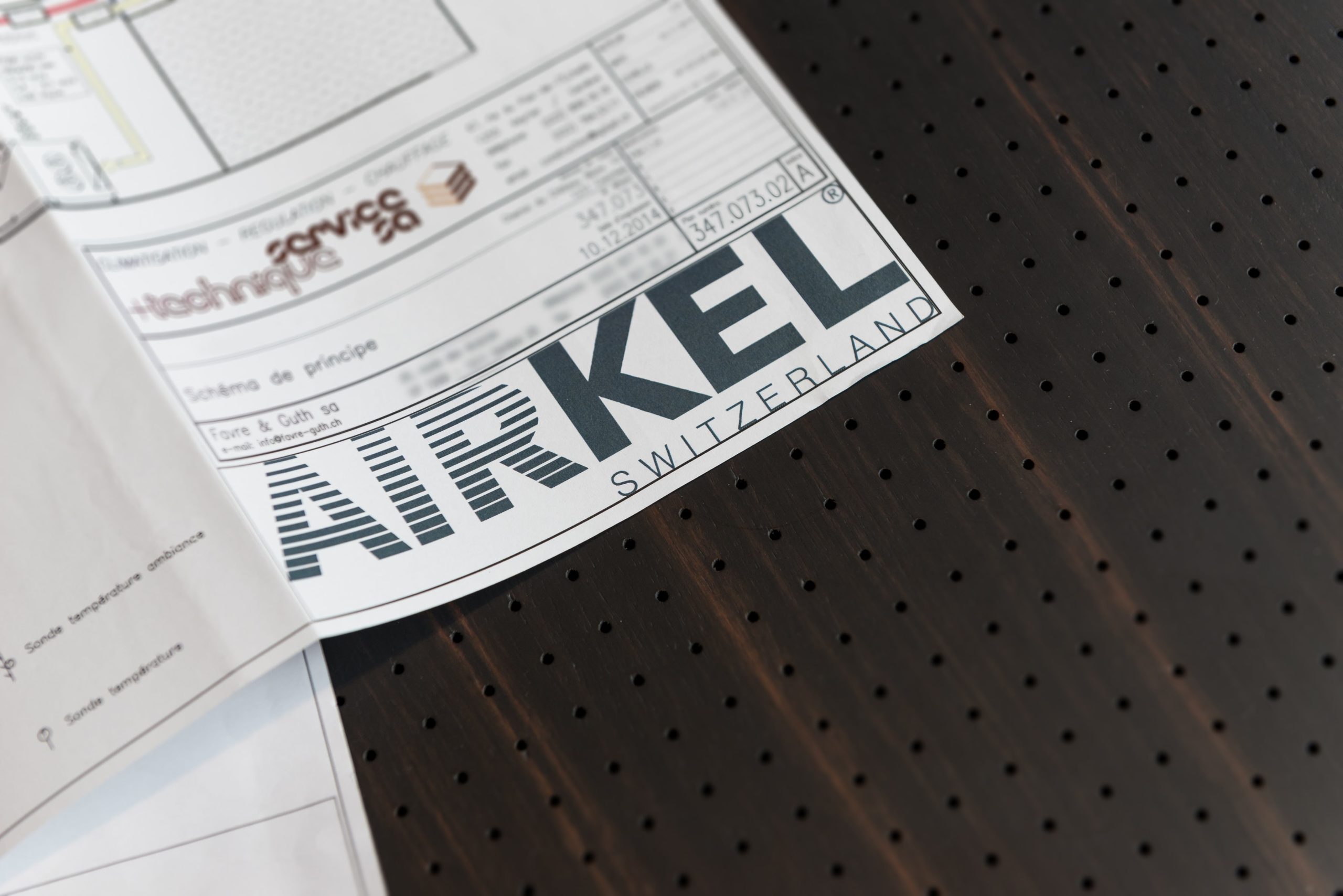
Delivery and Installation of the Machinery
In Switzerland
We will deliver and install the equipment necessary for the lounge to function. This work is based on the prior analysis. In the meantime, the floor and ceiling are selected (by the customer) and sent to production.
Overseas
The delivery and installation will be handled by the local team in charge of engineering in the building. Our engineers will provide them with the established guidelines and oversee the whole process. In the meantime, the chosen floor and ceiling are sent to production. This stage ends with an on site visit of our engineering team before delivery of the floor and ceiling in order to certify the quality of the installation.
Floor and ceiling delivery and assembly
Once all the prerequisites are met, the floor and ceiling are delivered and assembled by our assembly team. The quality control instruments are set up and the software is linked to the installation. During this process, we make sure everything is optimized, ensuring the efficiency of the system.
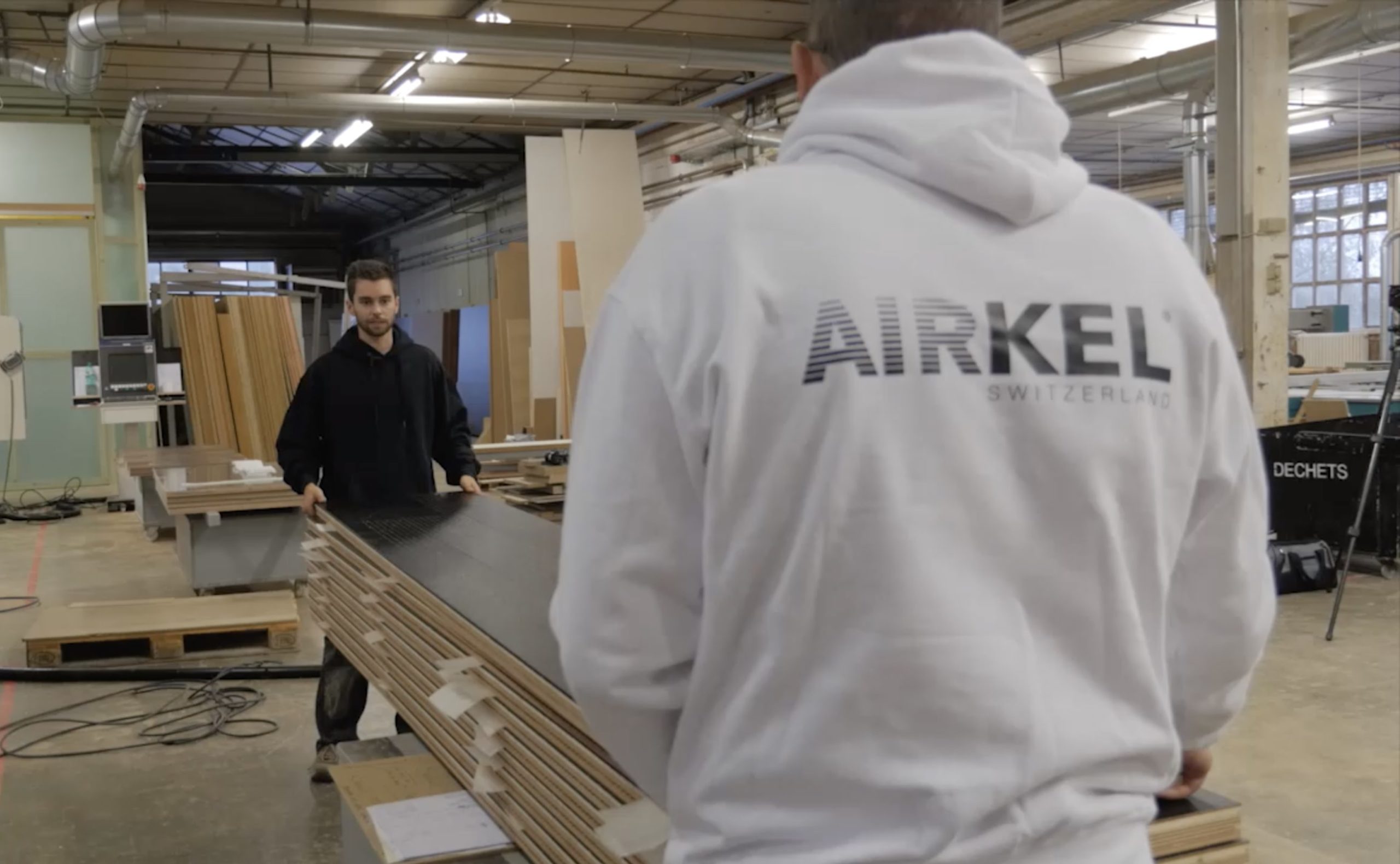
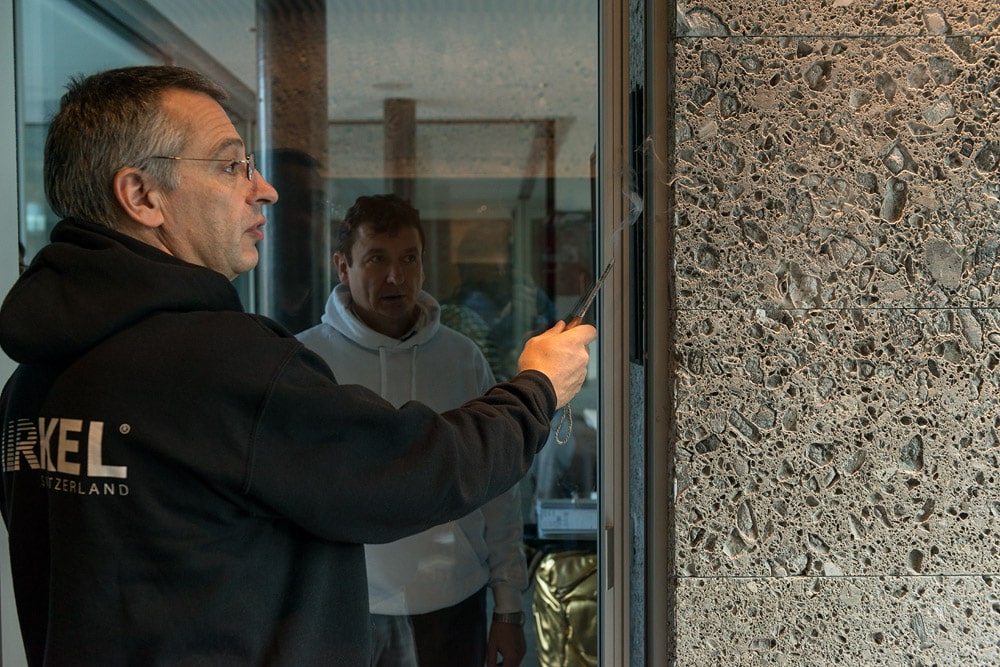
Commissioning
Once everything is set up, a final on site meeting is necessary in order to ensure the correct functioning of the system. At this point, the lounge is ready to function at its fullest capacity. The installed software can be used for two purposes :
- Monitoring only
- Regulating the installation
In either case, we will be able to supervise the running of the system, securing its sustainability.
Partners
Project Practicability
First contact and evaluation of the feasability of the project.
Analysis
Risk assesement and establishement of the conduct of the entire project
Machinery
Delivery and installation of the machinery
Floor and Ceiling
Delivery and assembly of the floor and ceiling
Commissioning
Software tuning and overall control of the entire installation
Project Practicability
Provided with sufficient data on the project, we are able to estimate the feasibility and the price of the system. The information required is as follows :
- Lounge dimensions (including usable height)
- Information on the upper and lower floors
- Total number of floors in the building
- Information on the technical room
Analysis
For existing constructions the risk assessment and building analysis require an on site visit from our engineering team (If the edifice is not built yet, we will work with blueprints). We will then implement a guideline for the project consisting of :
- Required specifications
- Checklist with benchmark measurements
- Block diagram
- Design of the built-in monitoring software
Delivery and Installation of the Machinery
In Switzerland
We will deliver and install the equipment necessary for the lounge to function. This work is based on the prior analysis. In the meantime, the floor and ceiling are selected (by the customer) and sent to production.
Overseas
The delivery and installation will be handled by the local team in charge of engineering in the building. Our engineers will provide them with the established guidelines and oversee the whole process. In the meantime, the chosen floor and ceiling are sent to production. This stage ends with an on site visit of our engineering team before delivery of the floor and ceiling in order to certify the quality of the installation.
Floor and ceiling delivery and assembly
Once all the prerequisites are met, the floor and ceiling are delivered and assembled by our assembly team. The quality control instruments are set up and the software is linked to the installation. During this process, we make sure everything is optimized, ensuring the efficiency of the system.
Commissioning
Once everything is set up, a final on site meeting is necessary in order to ensure the correct functioning of the system. At this point, the lounge is ready to function at its fullest capacity. The installed software can be used for two purposes :
- Monitoring only
- Regulating the installation
In either case, we will be able to supervise the running of the system, securing its sustainability.